New innovations need a supporting ecosystem to realise their value. The ambition of full electrification of vehicles has a downside. The vehicles are dependent on batteries for energy storage – and the production of these is energy intensive, produces high volumes of CO2 and requires mining of scarce metals.
Peter Carlsson, CEO and Co-Founder of Northvolt, was previously developing supply chains for Tesla when he realised the paradox in the industry. He described how Northvolt is using technology to transform electrification at the 2024 R&D Management Conference.
World’s first fully circular gigafactory
At that time battery cell manufacture was primarily in China; the value chain was very energy intense and released high volumes of carbon dioxide.
Manufacturing the average battery generates 100-150kg CO2 per equivalent KWh of battery capacity, and the car industry is producing 90 – 100 million vehicles a year. Electrification could potentially create a new carbon footprint for the industry, equivalent to half that of Germany.
There had to be a better way. This led to the development of Northvolt, the world’s first fully circular gigafactory using renewable energy to produce the world’s greenest battery with 75% lower emissions.
This is to be achieved by combining active cathode manufacturing with cell manufacturing and locating the facility in a site with abundant, affordable renewable energy.
Reducing the carbon footprint by 70%
The technology transformation is not just in production. In parallel, the company is creating the largest recycling centre to extract cobalt and nickel from the batteries, and a separate facility for lithium, with the aim of achieving 90% extraction. The intention is that batteries will have a life expectancy of 15 years, after which the new batteries will only have 15% prime material.
The facility recovers battery-grade metals with a carbon footprint 70% lower than mined raw materials, thereby enabling a fully integrated, circular battery production setup that has not previously existed outside of Asia.
The company is also reviewing the production process of graphite, which is a key ingredient for anode production. Currently 85% of significant production is in China, and is produced by graphitizing petroleum coke at 2,500° C. North Volt is researching the potential for synthesising wood fibre using electrolysis.
First Prussian White-based battery
Furthermore, the company is exploring alternatives to LFP (lithium iron phosphate battery) such as using salt to produce a sodium-ion battery. It has so far achieved LFP-type energy density, with the benefit of a very local supply chain.
Prussian White (PW) offers a promising cathode material for sodium-ion batteries and is free from lithium, nickel, cobalt and graphite. Leveraging a breakthrough in battery design and manufacturing, Northvolt plans to be the first to industrialize Prussian White-based batteries and bring them to commercial markets.
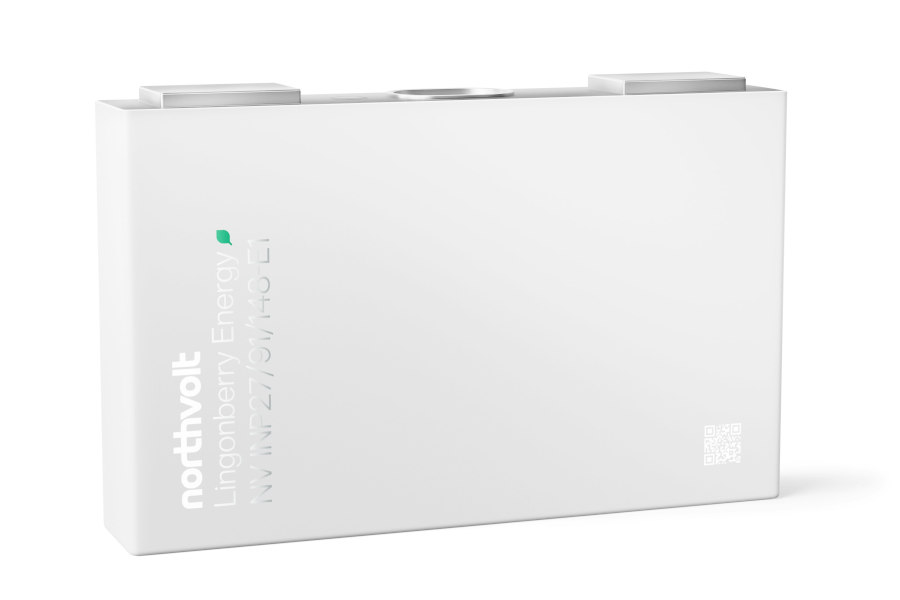
Innovative business model and digital blueprint
The Northvolt facility is being partly financed on the back of long-term off-take contracts amounting to over $55 billion, with partners including BMW, Scania, Volvo Cars and Volkswagen Group.
Scale-up of the facility is being achieved by building a model around the digital blueprint.
AI and simulations are able to manipulate 16,000 manufacturing parameters – too many for a human. This creates a huge opportunity to shorten the R&D cycle and create new types of chemical composition.
Peter concludes: “The digital blueprint ensures competitive edge – we know we have designed a great cell before making it.”
Find out more at northvolt.com